Precast Concrete Elements
References: R Record keeping requirement | E An engineering/certification requirement | P A permit to work requirement | S A safe work method statement (SWMS) / written plan
Hazards and Risks
Potential hazards and risks include, but are not limited to:
- Crane collapse
- Unloading
- Lifting equipment failure
- Panel / prop collapse
- Unauthorised entry
Design & Planning
R A risk workshop must be conducted with the subcontractor in relation to precast concrete element delivery, unloading, storage and installation.
Risk workshops should consider the following:
- Crane selection, access and siting
- Crane lifting capacity and operating radius
- Ground support conditions and the location of any excavations or underground services likely to be adversely effected by imposed crane loads
- Erection sequence of panels as specified on the shop drawings
- Site access points and erection areas to deal with crane and truck movement
- Site limitations and local street access
- Proximity of overhead power lines
- Lift plan
- Selection of lifting gear including, if rotation is to be carried out, the appropriate snatch block for rotation of concrete elements while suspended
- Protection of the general public
- Grouting of dowels
Compliance with AS 3850.2 Prefabricated Concrete Elements and National Code - Tilt up & Precast Concrete Elements in Building. Copies must be available on site.
E Design and shop drawings must be in accordance with AS 3850.2 section 2. A Qualified Person (structural engineer) must review and sign off on the design and shop drawings. For further information refer to the Construction Handbook.
The manufacture of the panel must be accordance with AS 3850.2 section 3 and permanently marked with an individual identifier and date of casting for each panel.
Manufacturer’s certificate of compliance (Birth Certificate) must be provided for all individual precast panel or elements delivered to site and reviewed prior to erection.
E The temporary bracing (and its design) must be in accordance with AS 3850.2 section 5. Any variation to bracing requires the written approval from a Qualified Person (e.g. engineer).
Racking systems must be designed by a Qualified Person (engineer) for the size shape and weight of the concrete element.
E A Qualified Person (engineer) must review and sign off (where applicable)
- Prop systems have been designed to resist all expected loads
- The proprietary documentation that sets out the safe use of a component or component system
- Prop connection methods have been detailed
- Prop bolt torque requirements have been specified
- Rigging diagram is incorporated into drawings
- Erection sequence methodology including stitch plates, bracing of the panels incl. temporary propping and details of any anchorage design or brace layout plan.
R The following documentation must be reviewed and maintained on site by MPX
- Erection sequence methodology indicating all temporary propping and/or bracing requirements with witness and hold points
- Modification approval plan where applicable
- SWMS/s (delivery, unloading, lifting, propping etc.)
- Lift study/plan (crane contractor) for each panel
- Traffic management plan (delivery, site/work area)
- WA - Notification to the Commissioner, intention to manufacture concrete panels
R WA and VIC - A Precast concrete elements checklist must be completed.
Training
R People carrying out precast concrete element construction work must be inducted into applicable SWMS and hold valid records of competency / training, evidence must be retained on site, refer to:
- Training and Competency Schedule (MPX and Subcontractor Supervisors, riggers, crane operators etc.)
Operational
S A task-specific SWMS is required for precast concrete work.
P WA - Permit to work Pre cast concrete elements must be implemented.
Entry into the area of precast concrete work or other work must be limited to persons directly involved in the process, or a person authorised by MPX or the precast erection subcontractor or regulator (WA).
Delivery and Storage
Delivery of concrete elements must be coordinated with MPX.
Prior to unloading concrete panels, lifting equipment must be inspected by the rigger.
A suitable means of access must be provided, for people performing rigging work to unload concrete elements.
Each concrete element must be individually secured and not be released until the crane has taken the initial load of that element.
Unloading of concrete elements must be sequenced such that the vehicle, racking system and other concrete panels remain stable at all times.
E If required, concrete elements are only to be stored in a position approved by Qualified Person (engineer).
The cranage, temporary storage and erection of concrete elements must be in accordance with AS 3850.2 section 4.
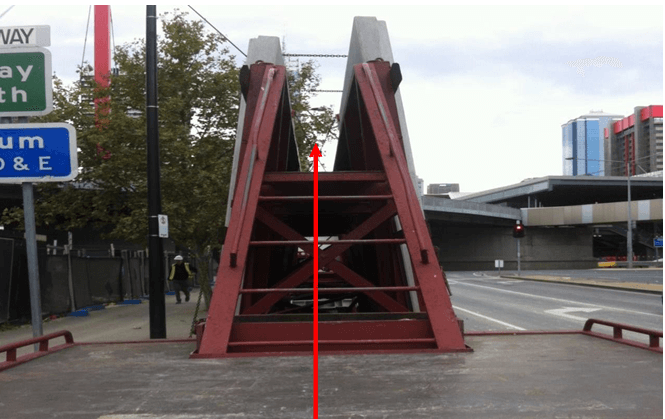
Cranes and lifting
Mobile cranes and lifting must be in managed in accordance with:
- Section: Cranes Mobile
- Section: Cranes Hoists and Other Lifting Equipment
- Section: Overhead Works Coordination
- Section: Plant and Equipment.
P NSW, QLD and WA - Where mobile crane is used, Outrigger Permit must be implemented - Crane lifting radius (Source: AS 3850 Tilt-up concrete construction)
Lifting inserts must be:
- Compatible with lifting clutches,
- Inspected prior to use, refer to
- Section: Cranes, Hoists and Other Lifting Equipment.
- Permanently marked with the nominal capacity in tonnes and the manufacturer’s identification mark which should be visible when the insert/clutch is placed in the concrete.
Lifting clutches must be:
- Identified on shop drawings
- Designed with a limit state factor of five (5).
- Proof tested to a load of twice the WLL
- Certified and individually identified by permanent marking or attachment of a durable tag before use.
- Inspected by the Competent Person (rigger) for wear and deformation before each use.
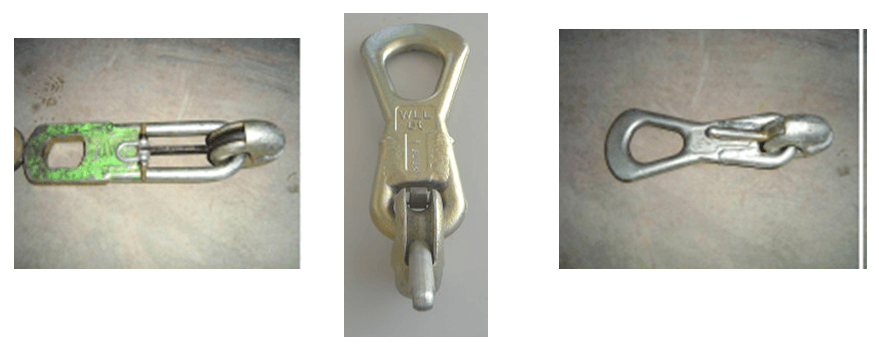
Erection
The method of erecting the panels must be assessed and documented, and installation and bracing of such panels should be in accordance with documented procedures compliant with AS3850 and specifications for proprietary items used.
Local wind speed must be monitored continuously by the crane operator and rigging crew. If conditions become hazardous, lifting and erection must cease, work and work area made safe and MPX site management notified
Clear access is to be maintained at all times and the work area is to be kept clear from unauthorised personnel, unrelated mobile plant/ plant /equipment and materials and overhead services, refer to:
The work area must be excluded by the use of signage and barricading, refer to:
- Section: Barricading and Signage.
Traffic management controls must be in place e.g. barricades, exclusion zones, spotters etc.
Element and footing strength must be confirmed prior to lifting and erection.
Fall zone established – minimum 1.5 times the panel wall height, clear of temporary amenities, public access areas must be barricaded.
Elements must be visually inspected for damage prior to lift – free from cracks and fractures along the face, openings and lifting insert points.
Rigging requirements for mid-air rotation should be as per figure below.
Levelling shims must be:
- Installed in accordance with the erection documentation
- On solid foundation, 40 mm [max. height] x 150 mm [min. length] x 100 mm [min. width] and be located at least 300 mm from the end of element/panel.
Braces - connected to panel before lift, minimum 2 per panel. Braces are required:
- To have an identification plate and load capacity marked
- Bee protected from potential impact incl. e.g. mobile plant and other site activity
- Installed in accordance with the erection documentation
- To be fixed to panels before they are lifted where possible
- To be torqued (incl anchors) to manufacturer’s specification.
- To be fixed at two third the panel height as per figure below
Knee, lateral and any additional bracing installed and secured immediately where required.
Stitch plates required to secure adjoining panels must be welded in accordance with the specification and AS/NZS 1554.
Strong backs to be fixed (where required) required prior to lifting.
Structural washers must be used with anchor bolts.
The element base must be secured on each panel as it is erected.
Locking pins must be secured on braces, such that a tool or key is required for removal.
Dead man anchors correct weight and position, where applicable.
Elements must be installed level and plumb.
The fixing of a concrete element for incorporation into a wall must be in accordance with AS 3850.2 section 6.
Work at heights is performed in accordance with:
- Section: Work at Heights
R If any remedial panel work is required it must be authorised, documented and completed prior to the riggers leaving site that day. Where this is not practicable the area and surrounding areas in which the elements are erected must be isolated until such time as the inspection is complete.
Post Erection
Concrete elements erected must be inspected by the Supervising Rigger at the end of each installation day, prior to the riggers leaving site.
Braced concrete elements, braces and brace bolts/ pins must be inspected visually by the subcontractor. and be maintained as required.
The removal of temporary bracing of a concrete element must:
- Be in accordance with AS 3850.2 section 76.
R Not undertaken unless written approval is obtained by a Qualified Person (structural engineer or erection engineer)
Damaged sustained to a panel or brace must be reported without delay to MPX.
Concrete elements and dowel pockets must be fully grouted unless otherwise stated in the erection documentation. For further information refer to the Construction Handbook.
Legal and Other Requirements
- AS 3850 Tilt Up Concrete Construction
- National Code - Tilt Up & Precast Concrete Elements In Building Construction
- Tilt up and Precast Construction Code of Practice (Qld) 2003
- Precast and Tilt-up Concrete for Buildings Industry Standard (WorkSafe Victoria)
Document Control
Version 1 August 2019 – New Standard
Version 2 September 2021 - Included references to the Construction Handbook for design drawings, shop drawings and grouting.