Perimeter Screens
References: R Record keeping requirement | E An engineering/certification requirement | P A permit to work requirement | S A safe work method statement (SWMS) / written plan
Note: This section is to be read in conjunction with:
- Section: Formwork
- Section: Work at Heights – General
- Section: Edge Protection
- Section: Fall Injury Prevention Systems (Fall Arrest / Fall Restraint)
- Section: Overhead Works Coordination
Informative
There are two types of perimeter screens, hydraulic screens (self climbers) and static screens (which are lifted by the crane/s)
Hazards
Potential hazards include, but are not limited to:
- Falls from heights
- Falling objects
- Adverse weather conditions
- Structural collapse

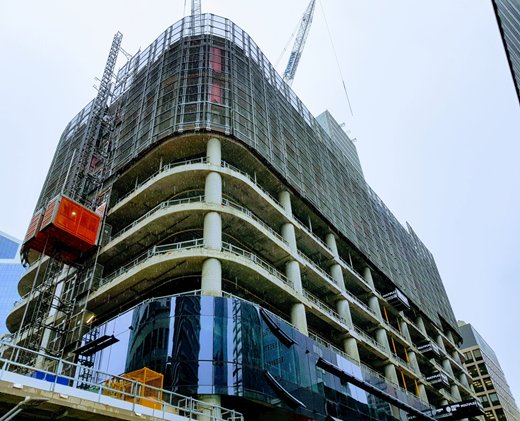
Design and Planning
- During design and planning, consideration must be given to delivery, assembly, installation, climbing/jumping, splitting and dismantle / removal and any other requirements as specified by the manufacturer / supplier. See Section: Risk Management.
E Perimeter screens must be:
- Designed by a Qualified Person (engineer)
- Detailed on up to date drawings/plans
- Designed allowing for site specific conditions including the buildings profile and effect of wind loadings as the height increases.
- Designed to provide sufficient structural redundancy such that the failure of a single fixing or connection point will not result in a catastrophic failure (see Recommended perimeter screen connection configurations - figures 2, 3 and 4).
Perimeter screen configuration (inc. trailing deck positions) must be drawn to scale for typical and non-typical levels of the structure to enable review and confirmation that the assembly, installation, climbing/jumping, splitting and dismantle / removal sequence does not result in any clashes, gaps or similar.
E Changes to the design of the perimeter screen must be authorised and signed-off by a Qualified Person (engineer).
- Perimeter screens must:
- Extend at least two (2) metres above the highest formwork deck
- Have SWL signage displayed on each working deck (where installed)
- NSW, VIC, WA - Have an identification number
Operational
S SWMS is required for perimeter screen, assembly, use, modification, and disassembly. SWMS are required to be submitted to MPX for review prior to perimeter screen activities.
R Workers involved in perimeter screen work are required to be inducted into the SWMS and trained in accordance with the manufacturers/supplier’s requirements.
- The screen crew must include a nominated person who is responsible for the direction and coordination of the assembly components and the lifting screens.
- VIC – The nominated person must be suitably trained and hold as a minimum a Basic Rigging (RB) HRWL.
- Workers involved in rigging work associated with perimeter screens must hold at least a Basic Rigging (RB) HRWL. Refer to:
- Training and Competency schedule
R Perimeter screens and associated components must be installed and inspected in accordance with engineering /manufacturer’s specifications, refer to:
- Plant and Equipment Schedule
E NSW, WA, VIC Critical elements (e.g. lifting points, needles) must have non-destructive testing (10% minimum) conducted prior to erection, records must be available.
- Perimeter screen mesh must be constructed from materials in accordance with design specifications
- The gap between the formwork/slab edge/floor and perimeter screen should be minimised as far as reasonably practicable and be protected by installing fixed plywood covers/flaps, rubber deflector shields or similar and be secured in position.
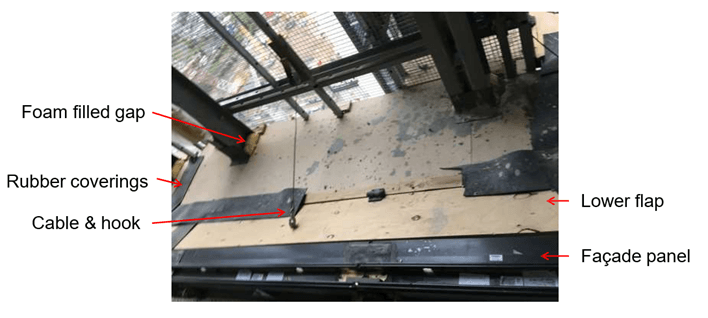
- Intermediate and trailing decks must be kept clean, free of debris / materials.
- A calibrated torque wrench must be used as specified for tightening/torquing of fasteners, a rattle gun or similar must not be used, over torquing fasteners causes stress, cracking or similar – refer to manufacturer / supplier specifications
- Prior to climbing or lifting screens:
- Concrete slabs must be confirmed as having achieved sufficient strength
- Any partial/or nonstandard deck that has been added to the screens must be removed
R Pre and post perimeter screen jump inspections must be completed and recorded by the formwork subcontractor and verified by MPX.
- Perimeter screen climbing / lifting operations must be constantly observed by a spotter allocated on each level and elevation. Where issues are identified that compromise the operation, the operation must be suspended.
- Two-way radio communications must be established between workers involved with climbing screens e.g., Supervisor, screen crew, crane crew and spotter(s).
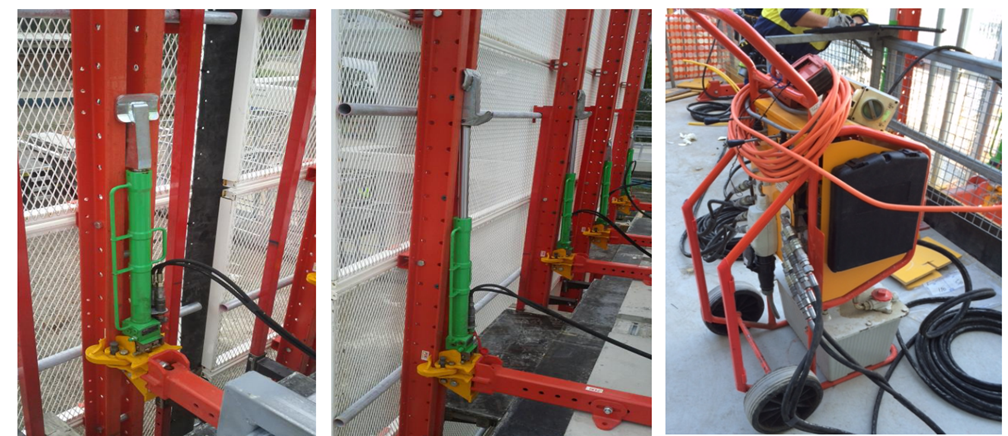
Legal and Other Requirements
- AS/NZS 4994.4 Temporary edge protection Perimeter Protection Screens
- WorkSafe VIC Perimeter Screens on Construction Sites
- QLD Formwork Code of Practice
- NSW Formwork Code of Practice
- Safe Work Australia – Guide to Formwork
Document Control
Version 1 August 2019 – New Standard
Version 2 August 2022 – Additional handbook references included along with requirements relating to design and planning, SWMSs, and competency requirements.