Ground Improvement, Piling, Anchors etc.
References: R Record keeping requirement | E An engineering/certification requirement | P A permit to work requirement | S A safe work method statement (SWMS) / written plan
Typical Foundation Types (Informative)
Replacement piles: These are typically piles which are put into holes dug or augured out of the earth. The concrete, or steel, simply replaces the earth, clay etc. which has been excavated.
Displacement piles: These are typically precast or pre-formed piles which are driven into the ground by a huge piling hammer. These displace the earth they are driven through.
Informative - Purpose of Ground Improvement
Piling transfers loads from a structure to a suitable rock or soil profile.
Ground Improvement (e.g. piling) is the practice of improving the soil profile (to carry loads) and slope stability.
Hazards
Potential hazards include, but are not limited to:
- Collapse or partial collapse of rig (or crawler crane) due to operation on unstable ground or ground which is not suitably compacted
- Off-sider / rigger being struck by rig or component
- Contact with utilities / services
- Entanglement in rotating parts (of rig)
- Crushing from moving materials
- Falls during maintenance and inspection (of rig), or into pile holes / excavations
- Falling objects/loads due to failure of lifting equipment
- Proximity hazards - overhead /underground services, adjacent structures
- Unexpected finds (hazardous materials, heritage items or latent ground conditions)
- Contaminated soil
- Excavated spoil contaminating clean fill.
- Over excavation
Design and Planning
E Building foundations must be designed and certified by a Qualified Person (structural engineer) taking into account information provided in the geotechnical report.
Selection of building foundations must take into account:
- The proposed structure and applied loadings
- The geotechnical and hydrological conditions
- Environmental conditions (including site contamination)
- Pile type and construction method
- Site constraints (access, location and storage) and
- Proximity to other affected assets (adjacent properties, areas of heritage significance, services assets).
E Geotechnical reports must be provided by a Qualified Person (geotechnical engineer).
E Geotechnical reports must provide information including, but not limited to:
- A summary of all subsurface exploration data, including soil / rock profile, exploration logs, laboratory / in situ test results and ground water information
- Interpretation and analysis of the subsurface data
- Geotechnical management procedures
- Engineering recommendations for design and construction.
R A risk workshop should be held for ground improvement activities, piling and anchoring on the project. The risk workshop must be attended by MPX project and subcontractor representatives. The workshop must be documented and include but not be limited to review of:
- Geotechnical reports
- Ground improvement / piling techniques
- Plant and equipment selection
- Crane selection and its configuration, capacities, expected loads, access / working radius requirements.
- Piling platform design (i.e.piling mat)
- External and internal traffic management – delivery/removal of rig and associated plant/equipment/materials, site access, oversize loads, movement curfews, pilot vehicles, potential constraints etc.
- Rig assembly process
- Lifting equipment
- Coordination/interaction with other site operations
- Proximity hazards public, roads, railways, underground / overhead services, in ground structures/existing anchors etc.
- Protection of public roads/infrastructure/adjacent structures/public
- Environment – spoil / contamination, unexpected finds (hazardous materials or heritage items), dewatering requirements
- Working hours / noise / neighbours
- Monitoring requirements – noise (neighbours/local council) and vibration (effect on adjacent structures/properties/heritage)
E Piling foundation documentation must comply with requirements specified in AS: 2159 Piling design and installation.
S SWMS are required for ground improvement, piling and anchoring activities. SWMS must be submitted to MPX for review prior to commencement of ground improvement activities.
S Reinforcement cages must be designed and constructed with welded reinforcement bars to the spirals (stirrups and ligatures).
When selecting couplers for Glass Fibre Reinforced Polymer (GRP), soil nails or rock bolts, the following should be considered:
- Take into account the specific design requirements and load conditions of the project ground conditions.
- Refer to the load capacity information provided by the manufacturer.
- Determine the appropriate coupler length based on the desired load-bearing capacity.
Training and Competency
R Workers carrying out piling and ground improvement activities must be inducted into the applicable SWMS, hold valid records of training / competency and applicable HRWL, refer to:
The piling subcontractor must verify that the piling rig operator/s is/are competent to operate the rig and are familiar with the attachments being used to carry out the piling work.
Plant and Equipment
R All plant and equipment must be registered by MPX and all relevant checklists and associated documentation completed and submitted prior to use on MPX projects
All plant and equipment used in ground improvement, piling, anchoring etc. must be in accordance with:
- Section: Electrical
- Section: Cranes, Hoists and Other Lifting Equipment
- Section: Plant and Equipment
- Section: Traffic Management
Piling Platform (Pile mat)
E A Qualified Person (i.e. or Geotechnical engineer) must specify (for the piling platform and any associated access ramps), the material to be used, thickness and compaction requirements.
E The piling platform must be certified as compliant with the engineering specifications prior to the assembly or operation of piling rigs and any associated mobile crane. Typically a piling mat certificate is provided by the piling contractor and the certificate confirms the piling platform is:
- Constructed of the specified material (e.g. limestone) to the specified thickness (e.g. 300 mm)
- The specified compaction has been achieved. (e.g. compaction of the limestone verified by nuclear density test and sand substrate below verified by a calibrated penetrometer).
- Note: Compaction testing must be provided by a NATA accredited laboratory.
The piling platform and any associated access ramps must be constructed to allow piling rig access to all areas where piles/anchors are being installed.
Steel reinforcement (cage) projection must be considered in relation to the piling platform level in regard to access, safety and quality.
The piling platform must be monitored and maintained (against specifications) throughout piling activities. Where the pile platform is noted to have been damaged or otherwise compromised, the piling platform must be repaired and recertified prior to continuing piling activities.
Assembly, Commissioning and Maintenance of Piling Rig / Crane
P For each mobile crane and piling rig the appropriate Permit / form/checklist must be completed.
Cranes and piling rigs assembled on site must be assembled by a licensed rigger/s/doggies and crane operator who are experienced in assembly of the specific crane/rig make and model. Assembly must be in accordance with the manufacturer’s specifications.
R Commissioning documentation must be provided to MPX prior to use of the crane / piling rig.
Where required to inspect, service or maintain a piling rig, a boom-type MEWP should be used in lieu of a work cage.
P WA -Where a work cage is used, a permit to work must be implemented.
Piling Operations
P WA, NSW and QLD - Prior to setting up a mobile concrete boom pump, an Outrigger permit must be implemented.
Exclusion zones consisting of hard barricading and signage must be established around piling operations, refer to:
- Section: Barricading and Signage.
Where applicable, excavation work must be in accordance with:
- Section: Excavation.
Communication methods must be agreed between the supervisor, pile rig operator and offsider/s prior to commencement of piling operations.
P Any hot works associated with piling operations must be in accordance with:
- Section: Hot work.
- Hot works permit
Spoil removed during the piling process is to be segregated / stockpiled and either re-used or disposed of in accordance with soil classification information available in the geotechnical report.
Open pile-holes must be suitably protected/exclusion zone established, to prevent risk of falls etc.
Any exposed steel reinforcement must be capped or otherwise protected.
Where the reinforcement projects within the over pour, the pile should be isolated by wrapping in foam (or similar) and the ligature should be terminated below the pile cap.
Note: Isolation of the reinforcement enables the over pour concrete to be removed safely, more efficiently (than rock breaking) and is less likely to structurally damage the reinforcement.
Concrete, bentonite or similar used in the piling process must be discharged into designated bins / trays. Concrete or bentonite must not be discharged onto open ground. Spills must be cleaned up immediately.
Employees must follow Safety Data Sheet directions for use, handling, PPE and storage of concrete, bentonite or any other substance used in the process.
Concrete placement and concrete placing equipment must be in accordance with:
- Section: Placement Concrete
- Section: Concrete Boom Pumps
R The concrete mix design for any concrete pile must be verified by a Qualified Person (piling engineer).
Concrete must be placed in a controlled manner.
Any fixed plant associated with piling (e.g. bentonite or water tanks) must be suitably protected so as to eliminate risk of employees falling.
Ground Improvement Operations
Exclusion zones must be established around the plant / operations , refer to:
- Section: Barricading and Signage
Where applicable excavation work must be in accordance with:
Section: Excavation.
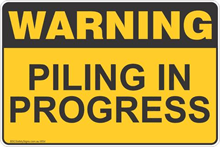
Dust must be suppressed (i.e. with water) during the mixing of grout and other ground improvement activities.
Grout and other ground improvement products must be used in accordance with the applicable SDS.
Where practicable, pallets of ground improvement products must be moved (by mechanical means) as close to the work area as practicable. Appropriate manual handling techniques must be utilised for movement of bags of grout and other ground improvement products, refer:
Excess grout (or other ground improvement products) used in the ground improvement process must be discharged into designated bins / trays.
Excess grout (or other ground improvement products) must not be discharged onto open ground. Spills must be cleaned up immediately.
Prior to excavation curing times for grout or other ground improvement products are required to be in accordance with the structural specification.
When performing Suitability or Acceptance testing of GRP soil nails or rock bolts, the following guidelines should be followed:
- Verify the calculated test loads have been reviewed by a Qualified Person (Structural Engineer) and that test loads do not exceed 80% of the Ultimate Tensile Strength (UTS) of the system under test
- Consider both the UTS of the GRP bar and the UTS of individual components that form the GRP soil nail or rock bolt system when calculating test loads, including couplers
- Verify the position of any couplers in the system has been coordinated and documented in a shop drawing, specific to the application, i.e. couplers are positioned within the grouted section of the system.
Legal and Other Requirements
- AS: 2159 Piling design and installation.
- Guide to Managing Safety – Piling Work & Foundation Engineering Sites 2014 (WorkSafe VIC)
- Excavation Work Code of Practice (Qld) 2013
Document Control
Version 1 August 2019 – New Standard
Version 2 November 2023 – New requirements have been incorporated on selecting and executing the suitability and acceptance testing for Glass Fibre Reinforced Polymer (GRP) soil nails or rock bolts.